What Is 3D Printing
Back in the old days one way to test out a physical design was to build it. If the cost of building the real thing was too expensive then you'd model the shape out of something more cost effective, like clay. And to be sure, the hands of a professional artist can be very, very good. But even the best human hands are only so good, what if you have some seriously rigid specifications for your model? What if you need accuracy down at the micrometer scale? Even if you think you've got the shape right, once your design hits the factory floor it's very costly if you find a flaw and have to stop production to re-tool the manufacturing process. This is how 3D printing got it's start, as a way to quickly prototype shapes using a cheap medium.
The first 3D printer was created by Charles W. Hull of 3D Systems Corporation in 1984. C.W. Hull is known as the father of the solid imaging process called “stereolithography” – or simply “3D printing” as we call it today. The Standard Tessellation Language (STL) file format invented by Hull is still widely in use today.
3D printers are machines that “print” three-dimensionally, CAD-rendered objects by precisely layering bits of material and then solidifying that material into a larger object. There are a number of ways that this is done, and the method chosen often depends on balancing price, material properties, and the speed and precision with which you can print:
Stereolithography (SLA)
This process is the oldest process, and the process first developed by Hull. This process involves converting a liquid plastic into a solid using photopolymerization, a process by which light causes chains of molocules to link together forming polymers. The light source used is usually produced by a laser. The laser light is moved around on the plastic to trace out a single layer of the model, then the model is moved up allowing more liquid plastic to seep in underneath and the layering process is repeated until the model is finished. Depending on the materials and methods used, once printed a model may require curing time under special conditions to finish the job.
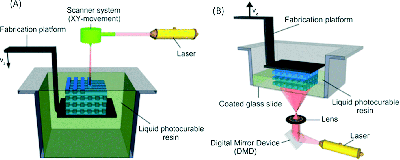
Pros:
Speed – Printing is fast.
Accuracy – Dimensional tolerance is +/- 0.1 mm (desktop) to +/- 0.01 mm (industrial)
Scaling – If you can build a tank big enough, and a gantry large enough to move your laser around, then you can make large parts.
Surface finish – Printed parts are nice and smooth.
Cons:
Limited material selection – Your material has to be a photo-sensitive, polymerizable liquid.
Materials are unpleasant – Special care must be taken to handle the materials. Home-grade SLA printing resins require the same handling as other household chemicals or adhesives, such as gloves and eye protection to avoid direct exposure. Materials are not environmentally friendly.
Models lack strength – Models are only suitable for display, prototyping, or light-duty functional use. This will likely change over time as new materials are developed with specialized properties.
Digital Light Processing (DLP)
Similar to SLA, DLP printing uses light to solidify a liquid plastic. The difference is that DLP uses a projection system to solidify an entire layer of the model at once.
TODO: FINISH THIS
Why Your Crazy IT Manager Thinks This Is Cool
Disclaimer
NIMBioS IT staff will not take responsibility for your personal machine. The reader is expected to know how to administrate his or her own machine.
The documentation above is merely for guidance. Menus, options, and commands presented may not match the reader's particular operating system, software, or versions.
None of these documents have a brain. Readers are expected to provide their own.